Best Practices for Making NPK Fertilizer
NPK fertilizer is a critical component in modern agriculture, providing the essential nutrients required for plant growth and development. However, with numerous production methods available, it's crucial to understand the best practices for making NPK fertilizer to ensure optimal crop yields and soil health. This article delves into the essential steps and considerations for creating high-quality NPK fertilizer.
1. Selection of Raw Materials The first step in NPK fertilizer production is selecting the appropriate raw materials. The most common sources include ammonium sulfate, potassium chloride, and superphosphate. It's essential to choose high-quality raw materials to guarantee the desired nutrient content and minimize impurities.
2. Crushing and Screening Once the raw materials are selected, they must be crushed and screened to the appropriate particle size. This process ensures that the nutrients are evenly distributed throughout the fertilizer, promoting better plant uptake.
3. Mixing After crushing and screening, the raw materials are mixed in the correct proportions to achieve the desired NPK ratio. It's important to use precise weighing equipment to ensure accurate mixing.
4. Granulation Granulation is the process of converting the mixed fertilizer particles into larger, more uniform granules Granulation Granulation is the process of converting the mixed fertilizer particles into larger, more uniform granules
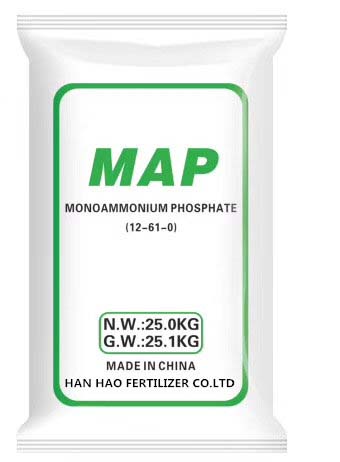
Granulation Granulation is the process of converting the mixed fertilizer particles into larger, more uniform granules Granulation Granulation is the process of converting the mixed fertilizer particles into larger, more uniform granules
best making npk fertilizer. This not only improves the handling and application properties of the fertilizer but also enhances nutrient release and availability to plants. Common granulation methods include drum granulation, prilling, and extrusion.
5. Drying and Cooling After granulation, the fertilizer must be dried to remove excess moisture and prevent bacterial growth. The drying process should be carefully controlled to avoid overheating, which can damage the fertilizer's nutritional value. Following drying, the fertilizer is cooled to prevent caking and ensure easy handling and storage.
6. Packaging and Storage The final step in NPK fertilizer production is packaging and storage. The fertilizer should be sealed in appropriate bags or containers to protect it from moisture, pests, and contamination. Proper storage conditions, such as dry, cool environments, are essential to maintain the fertilizer's quality and nutrient content.
In conclusion, following these best practices for making NPK fertilizer is essential for achieving optimal crop yields and soil health. By selecting high-quality raw materials, properly crushing and screening them, mixing them in the correct proportions, granulating them, drying and cooling them, and packaging and storing them correctly, farmers can ensure that their crops receive the necessary nutrients for healthy growth and development.